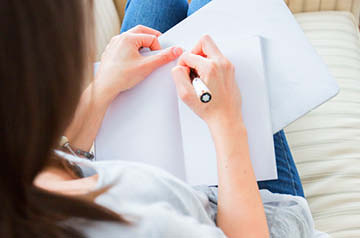
Planning major construction projects for health care organizations can prove incredibly challenging as your organization works to simultaneously meet current needs and future challenges that have yet to even present themselves.
Taking steps early on in the process to truly envision how new facilities will operate while also focusing on contracting strategies can help bring major advantages to the construction process and final product—potentially resulting in significant project savings and annual operating expense reductions.
With the COVID-19 pandemic continuing and its required safety precautions front of mind, concerns around budgets and operational standards can be even more prominent.
Using the lean methodology of 3P to envision the design and operations of your future space can help your organization design to those goals—and implementing proper construction contracting can help drive major cost savings throughout the process.
Below we explore an overview of 3P and how your organization can use it to navigate your planning processes.
What is Lean and 3P and How Does It Help?
Lean methodology is a performance improvement approach that originated in the manufacturing industry and subsequently revolutionized a range of industries, including health care.
The concept focuses on working toward continuous improvements by tapping into and empowering your frontline employees and building quality into processes.
3P—production, preparation, process—is a subset of lean that works to radically design or redesign processes, products, and facilities to better meet the demands of the health care marketplace.
Benefits of 3P for Creating New Facilities
Implementing 3P into your initial design processes can help ensure you’re addressing and supporting the varied needs of all parties who will interact and utilize your facilities, and that your project team—including architects and contractors—build towards those needs.
3P can help tap into big picture problems, but also acknowledge everyday concerns and allow you to:
- Better integrate care teams and enhance workflows and processes, improving customer, patient, and staff experience and potentially reducing annual operational spend
- Embrace and efficiently use new technologies
- Allocate spaces for universal versus designated needs
- Reduce motion waste
- Improve operational efficiencies and effectiveness
- Support safety and ergonomics for staff
Addressing Differing Staff Needs
Differing members of your staff may have concerns of which you may not even be aware that should be addressed up front.
For example, while gathering valuable information about patient and staff needs, nurses could request IT desks be placed in a spot that allows them to make eye contact with patients as they enter data to maintain and strengthen patient relationships.
Housekeeping staff could request specific locations for dirty linen and garbage cans to facilitate the removal of used items. Imaging could request specific door sizes, room layouts, and lighting to facilitate in-room imaging.
Instead of requiring ambulatory patients to travel to different departments, services such as lab draws and pharmacy could be co-located or pulled to patients, reducing their overall service time and improving their care experience.
Co-locating ambulatory care team members in a so-called shoulder to shoulder manner in close proximity to the exam rooms could enhance situational awareness.
COVID-19 Implications
With the emergence of COVID-19 in early 2020, organizations are paying greater attention to quality, safety, infection prevention practices, innovation, and additional challenges while adapting to changing conditions.
There have been many organizational shifts, such as the increase in telehealth, remote work, and other changes to minimize spread of the virus and to promote convenience for consumers.
While the lasting impacts of COVID-19 are still unclear, questions related to what the spaces of the future will look like and how they will be used are likely to emerge. Organizations should consider what requirements will be needed in both the near- and long-term and how expanding technologies could be incorporated into new spaces.
For more immediate concerns, the pandemic could pose challenges once construction is in progress. Organizations will want to ensure healthy work sites for crews by following necessary safety precautions and steps that will need to be taken to implement and adhere to them.
Lean can help organizations in many ways—from assessments of space utilization to methods for developing enhanced and reliable safety measures and business process adaptations and strategy that result in significant operational efficiencies and reduced annual operational spend.
How Does 3P Work?
3P takes place through a series of preparation sessions and workshops that typically include the following:
- Visioning Workshops. Visioning processes start by connecting with key leaders to understand where they want the organization to be in the future, how they hope facilities will operate, and what key issue they want to solve that aren’t being addressed by current processes or facilities.
- Design Workshops. With initial visions assessed, design workshops aim to spark creativity in leadership so they can envision what facility design and layout could actually look like, eventually landing on a consensus.
- Implementation Workshops. From there, leadership determine areas of the future state design that need defined focus and what goals need to be accomplished for the consensus vision to become reality.
What Contracting Strategies Should Be Employed Prior to Construction?
While 3P helps map out plans to keep projects moving efficiently and on time, strategically defining contracts with architects, contractors, and other involved parties can further help owners manage project budgets and control costs.
Specifically, contracting strategies should include the following:
- Competitive bidding procedures
- Contract-type selection
- Strong cost-of-work definitions
Competitive Bidding Procedures
Obtaining comparative bids on contractor and subcontracted work can help ensure competitive pricing for a complete project.
Pursuing three bids is often recommended to provide an effective comparison between bidders by driving cost competitiveness without being overly burdensome for either the contractor, owner, or developer.
Contract-Type Selection
Contract-type selection can be as critical to managing budgets as competitive bidding procedures. Understanding the different contract types available to your organization can help increase transparency and accountability between parties. The most common contract types include the following:
- Lump sum
- Time and materials
- Cost plus
- Cost plus: guaranteed maximum price (GMP)
Each contract type needs to be evaluated for appropriateness—especially with COVID-19 impacts and considerations—and aligned with a project’s scope and objectives.
Lump-sum contract types, if not properly procured, may include the following:
- Higher markups
- Increased change orders
- Inadequate material quality
Time-and-materials and cost-plus contract types that aren’t properly managed by an owner could encounter low productivity resulting in schedule delays and increased construction spend.
GMP contracts, on the other hand, could suffer from poor cost-of-work definitions that result in a lack of controls surrounding budget and cost.
Strong Cost-of-Work Definitions
Selecting strong cost-of-work definitions has many benefits when coupled with a GMP contract. A GMP contract allows owners and contractors to define adequate allowable and unallowable cost of work for a project, which helps both parties manage and control cost.
At the same time, cost-of-work definitions need to be sufficiently clear to enable the efficient validation of compliant project charges.
Important Contracting Language Considerations
Take these five important actions to help mitigate common project budget and cost risks through careful use of contract language:
- Clarify allowable and unallowable actual labor charges
- Include competitive subcontractor bid requirements
- Set rates and caps on contractor-owned equipment
- Define change-order reporting requirements
- Add a right-to-audit and accounting records section
Cost overruns can undermine the viability of any construction project. That’s why clearly defined contracts are essential—for all parties involved.
Engaging an experienced team of construction auditors can help align best practices with competitive-bidding procedures, contract-type selection, and cost-of-work definitions.
3P works to avoid having to make changes to plans during construction to appease potential conflicts or new ideas that may arise, however, clearly defined cost-of-work terms can also help avoid costly changes.
We’re to Help
To learn more about our services, including how 3P and our construction advisory can help with you meet your project goals and keep your project on budget and schedule, contact your Moss Adams professional.